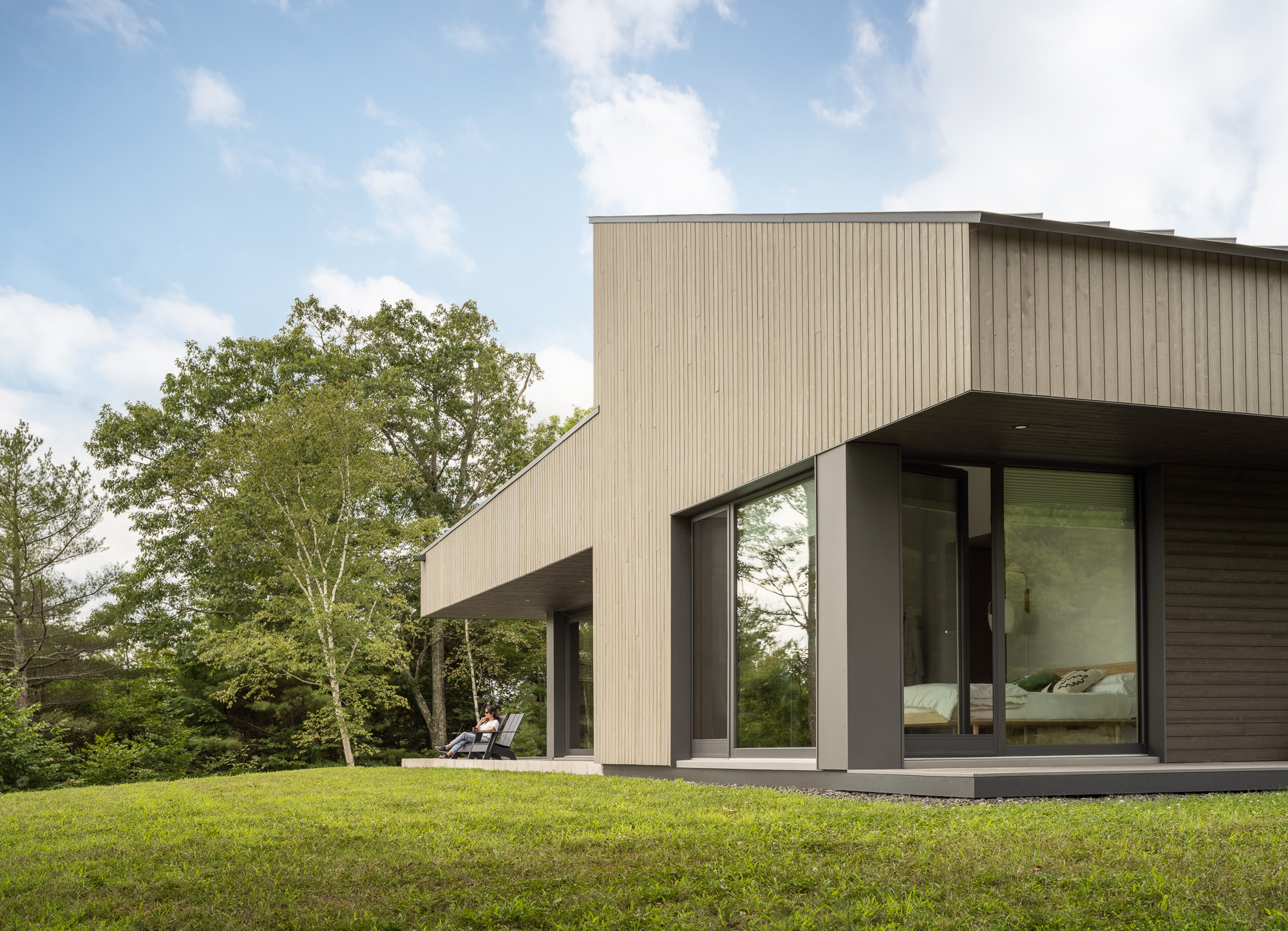
Advancing the next generation of building designs, materials and systems.
We do not believe in staying in our lane. We all face existential challenges given the rate of climate change and buildings play an outsized role in both the problem and potential solution. Therefore, as a minimum requirement, all buildings should not only be neutral or sustain the environment, but actively help improve the climate with solutions that are environmentally appropriate, durable and scalable.
We also believe that the golden age of architecture has not arrived and that design and construction solutions must actively evolve to meet the challenges and opportunities we face. Through innovation, entrepreneurship and collaboration, we are developing the next generation of materials, construction systems and buildings that have a scalable positive impact and can improve people’s lives and the planet.
Our approach to problem solving and innovation has always been based on data, and we apply that to a building’s energy performance, environmental footprint and construction costs to ensure the solutions we propose align with reality and are impactful. This has been a founding principal of the company and continues to guide our approach today. As leaders in building ecology and architectural design, we have not turned away from the difficult challenges and we will continue to take risks to help ensure that future generations can inhabit and enjoy this planet.
While many companies talk about innovation, we actually do it.
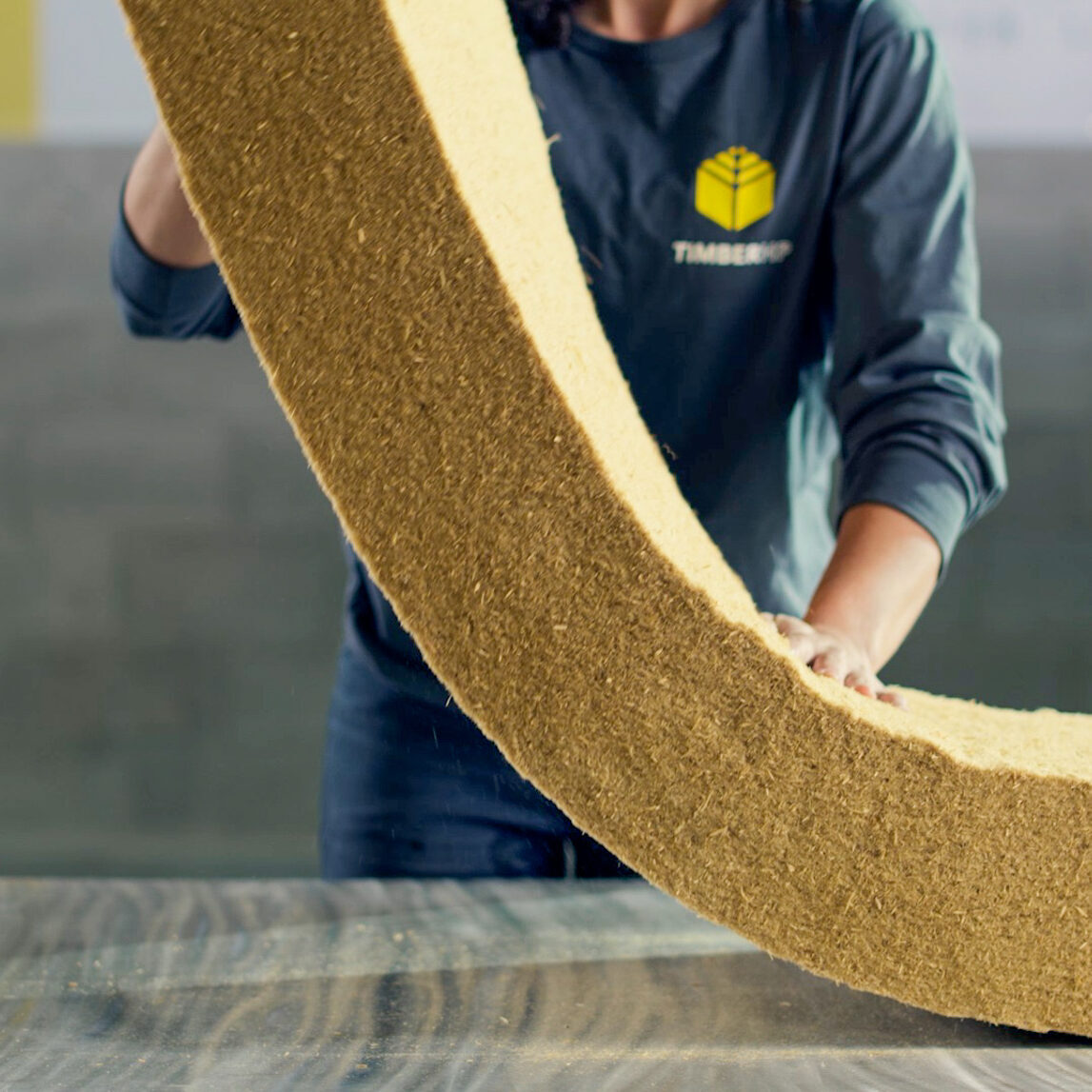
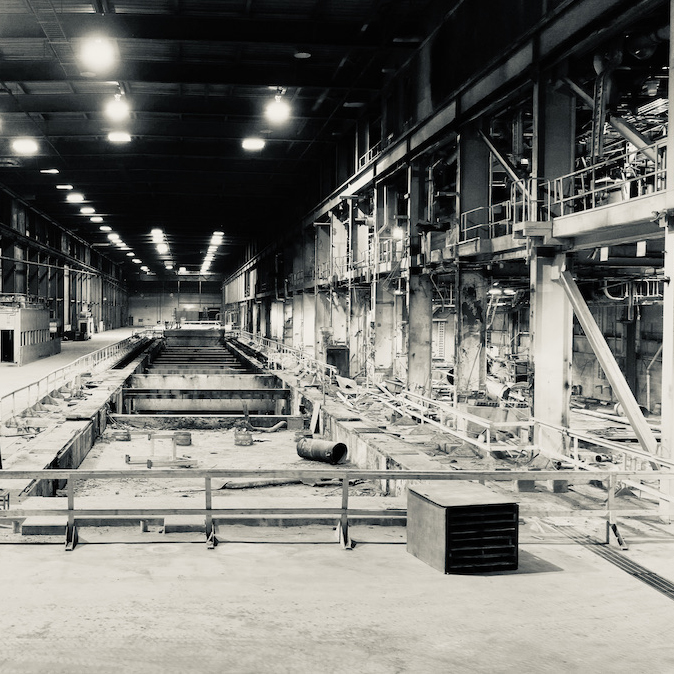
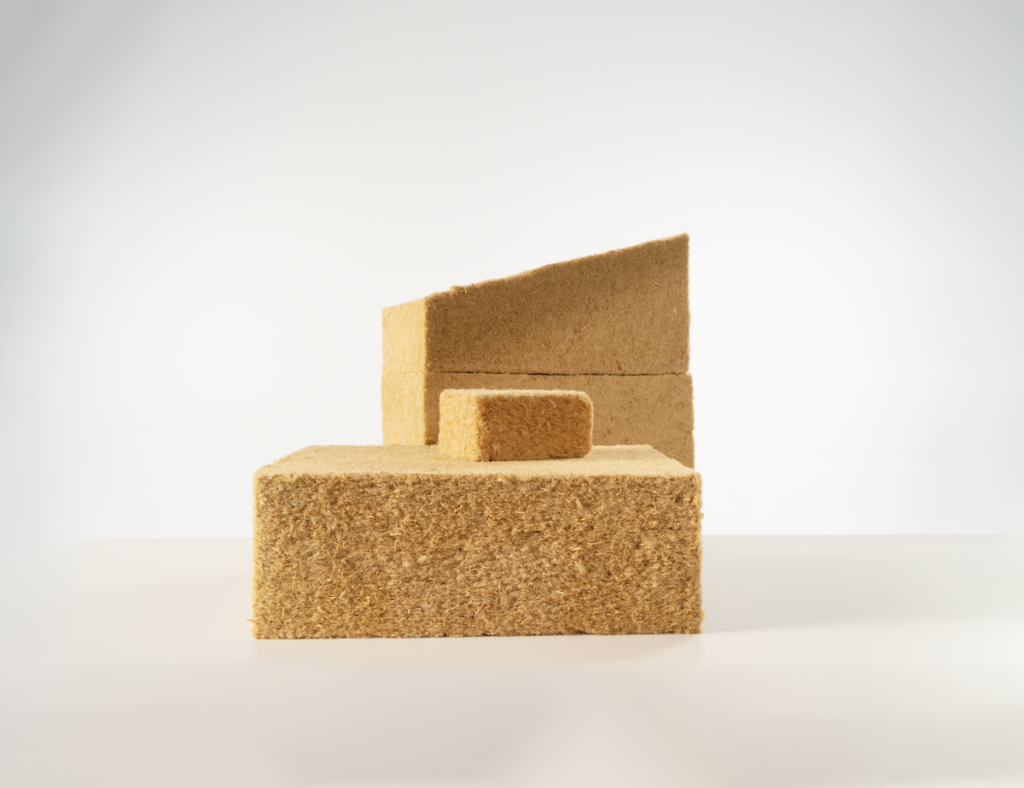
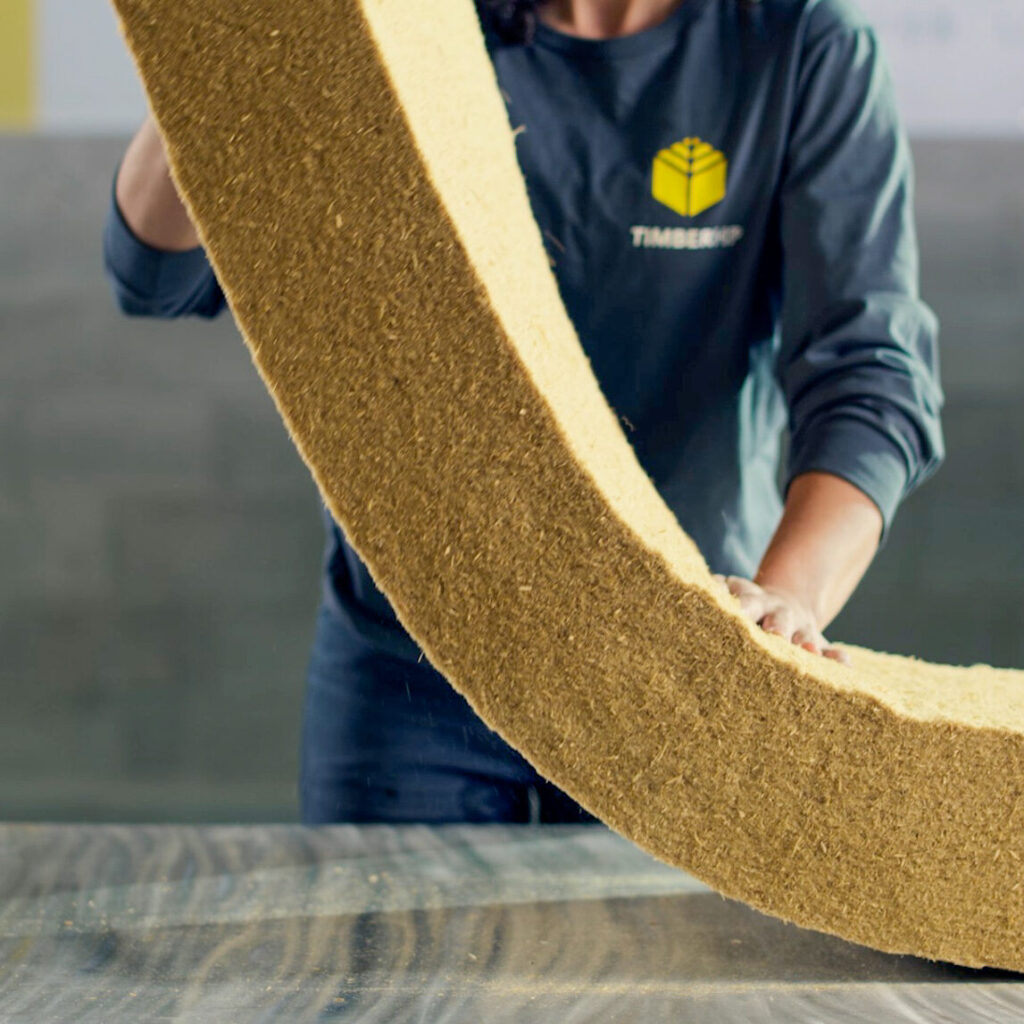
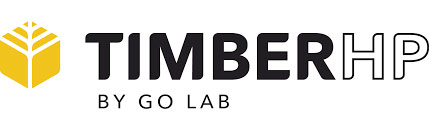
Wood Fiber Insulation Manufacturing in Maine
Insulation made from wood fiber has been on the market in Europe for 20 years, but our sister company, Timber HP will be the first domestic producer of wood fiber insulation, using a waste material from the lumber industry to produce cost-competitive replacements for the plastic foam and fiberglass products that currently claim the lion’s share of the U.S. insulation industry. Co-founded by OPAL executive partner Matthew O’Malia and materials scientist Joshua Henry, Timber HP is a clean-tech company building out its manufacturing facility for the next generation of insulation products that are renewable, recyclable, and carbon sequestering, located at the former paper mill in Madison, Maine.
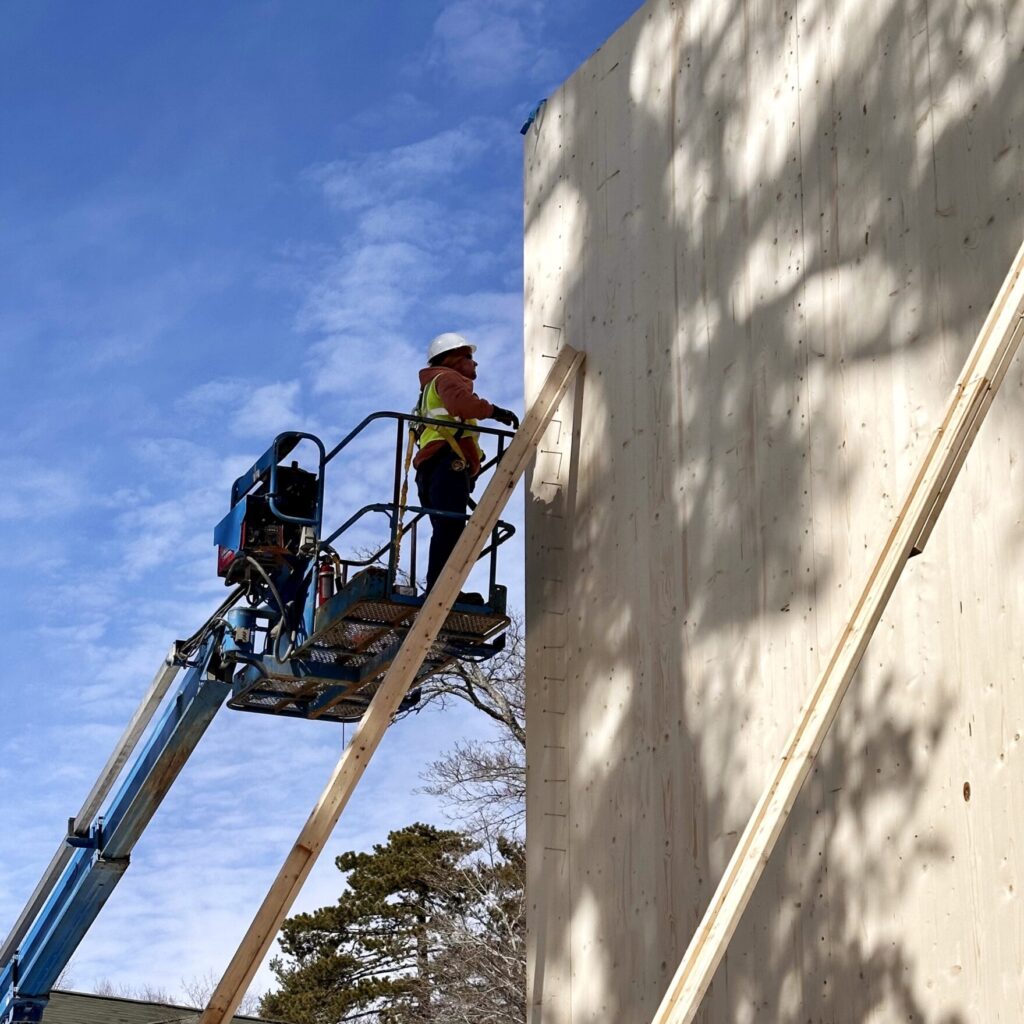
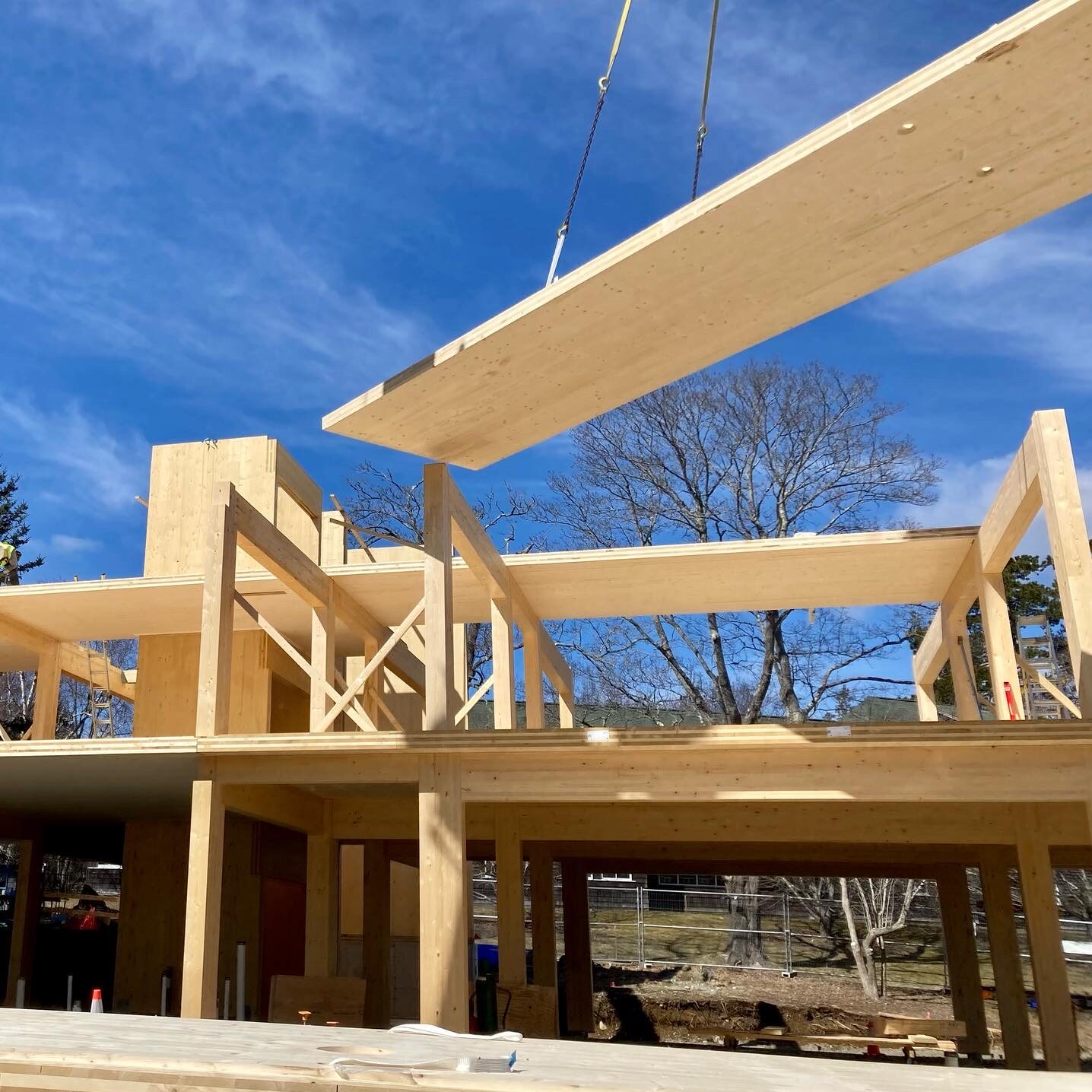
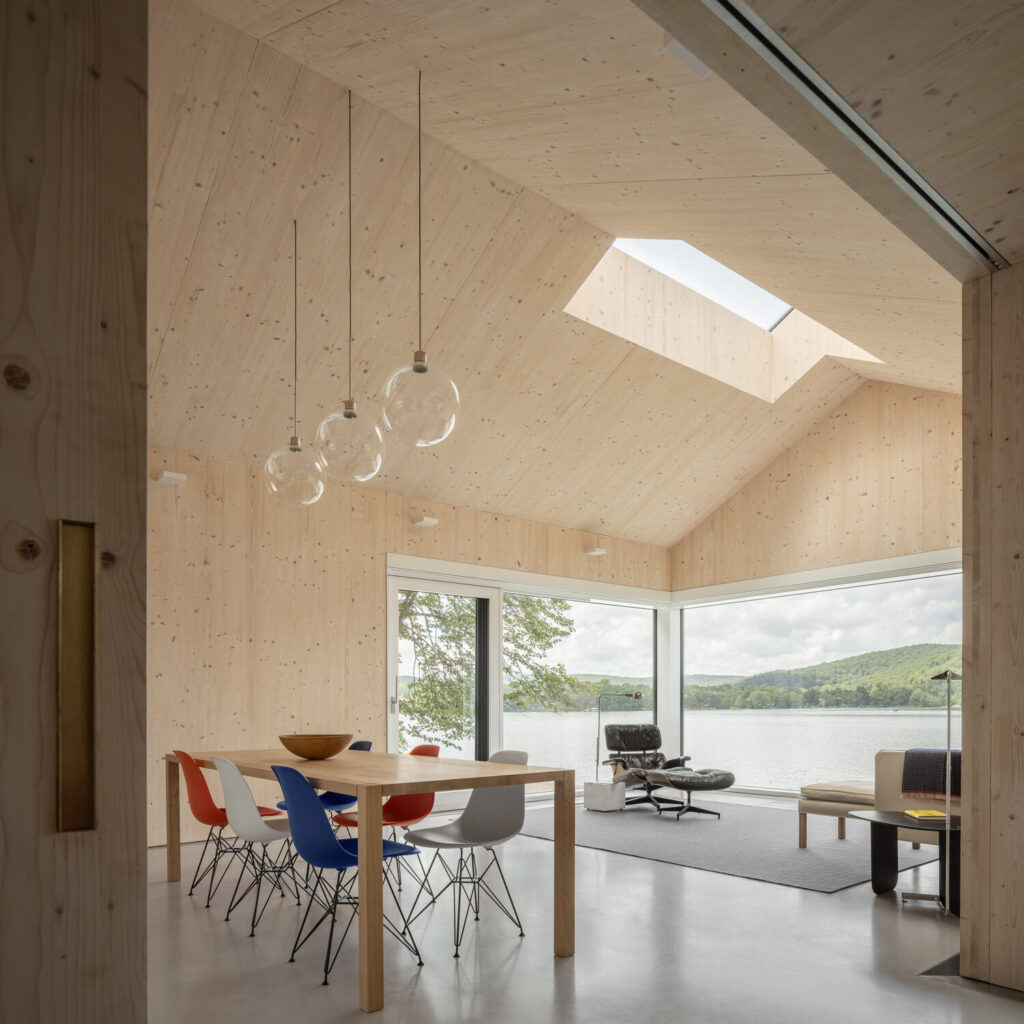
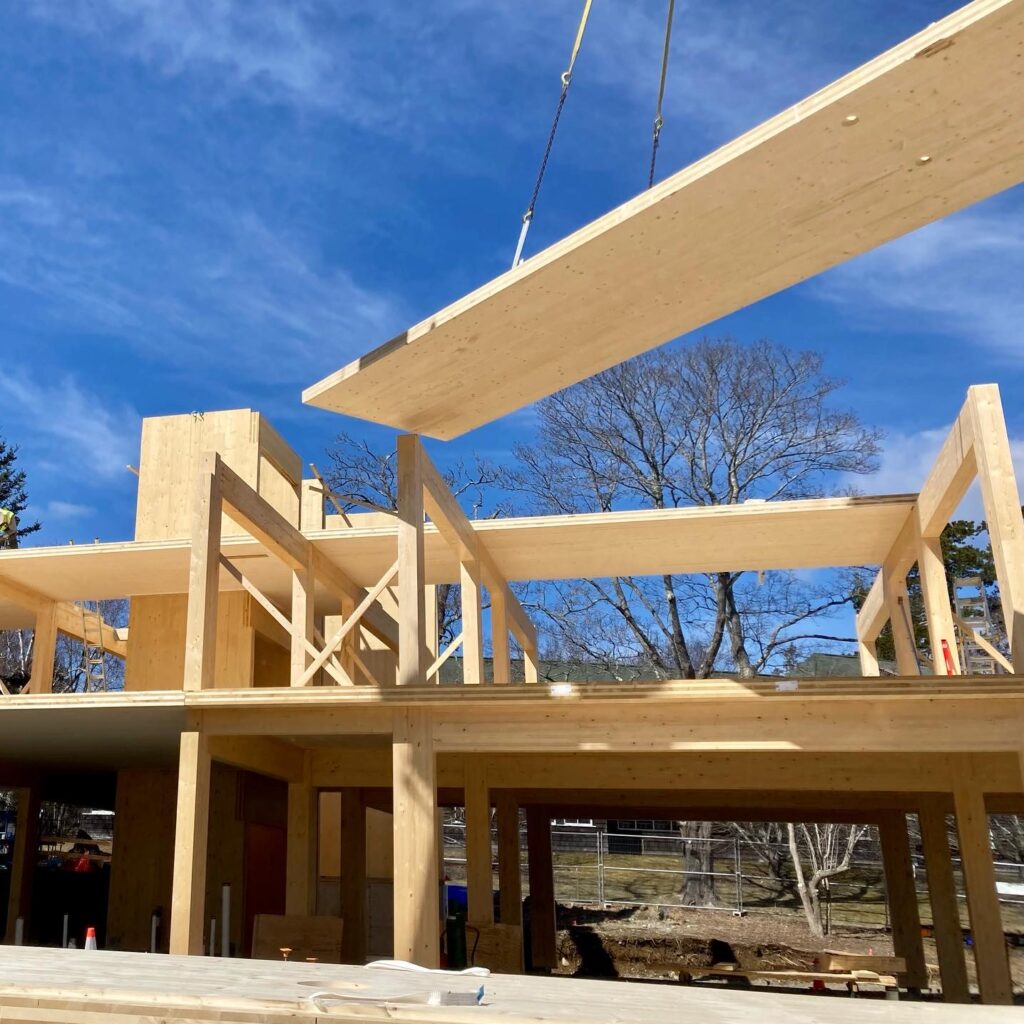
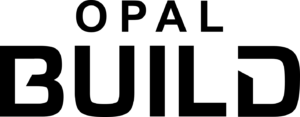
All Wood Construction
We founded OPAL with the mission of radically reconcieving the way buildings are made. After pioneering the adoption of Passive House design in North America, we created Timber HP, the next generation of sustainable, carbon-sequestering insulation. Our latest initiative—OPAL Build—represents another landmark step in that process, drawing on OPAL’s expertise in design and material science to develop an all-wood building shell system that sets new standards in construction efficiency, energy performance, scalability, and carbon-sequestering sustainability. Applicable to a wide range of building types, the OPAL Build system utilizes abundant renewable materials, employs fully developed manufacturing processes, and outperforms conventional methods, from stick framing to concrete-and-steel construction.
Improving buildings’ operational energy efficiency is a vital first step in addressing the climate crisis, but the job doesn’t end there. To radically reduce—or even erase—the total carbon footprint of OPAL buildings, we’re also working to zero out the carbon debt of the materials that go into their construction. In most applications, that means shifting from energy- and carbon-intensive building materials like fiberglass, foam, and concrete to those made from wood. Having established the efficacy of Passive House principles in minimizing a building’s operational energy use and carbon emissions, we believe it is now time to address the substantial hidden environmental costs of the materials that make up the building. This includes the crucial impact of embodied carbon, the carbon emitted during the manufacture, transportation, and eventual disposal of those construction materials.
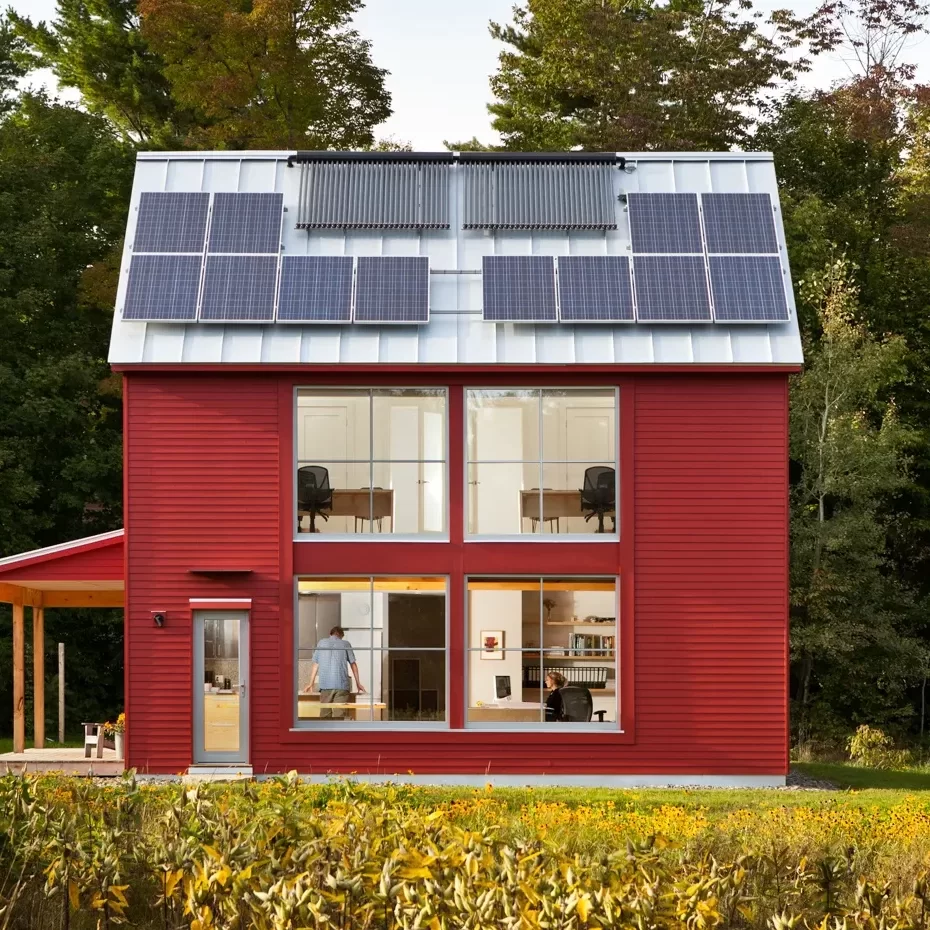
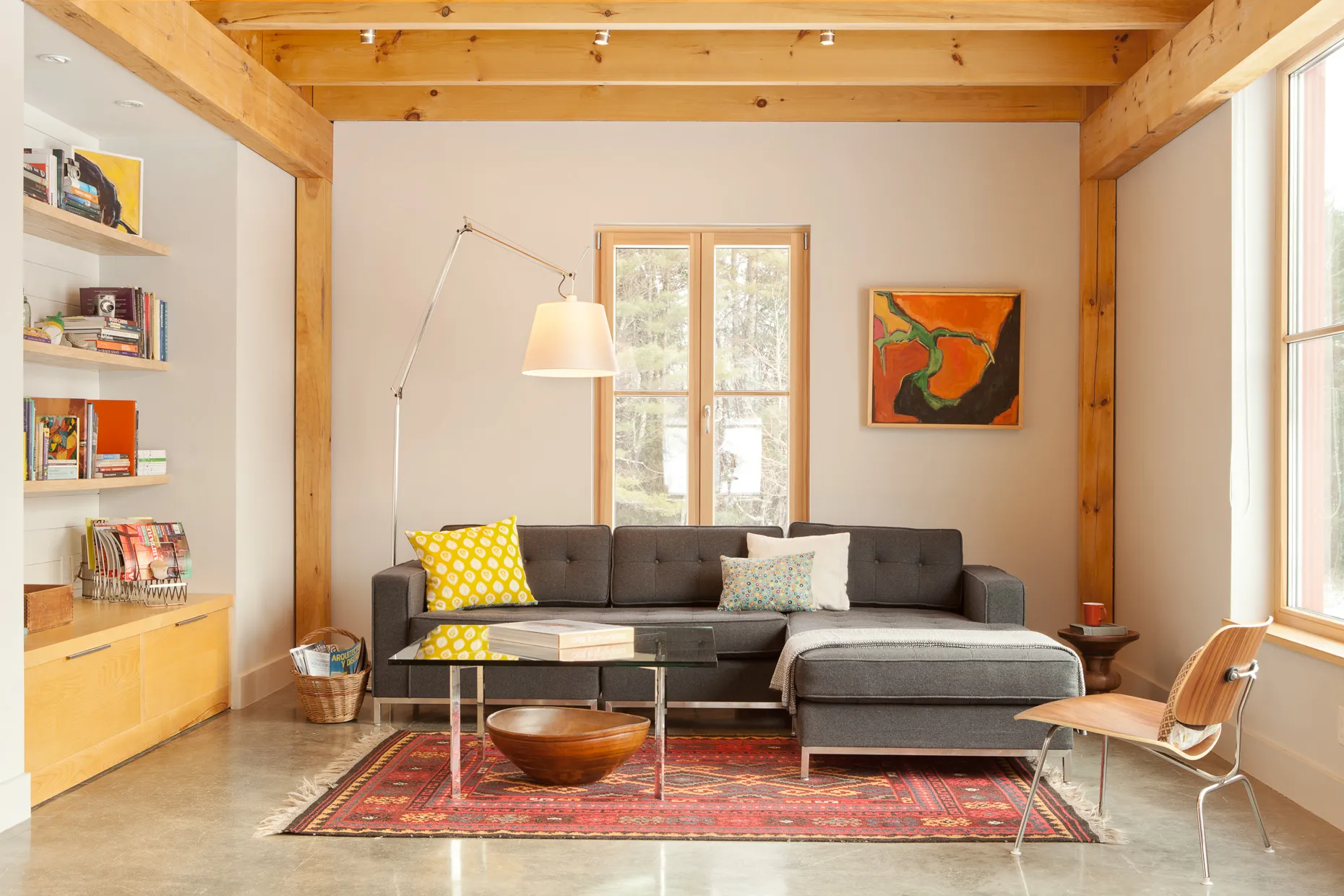
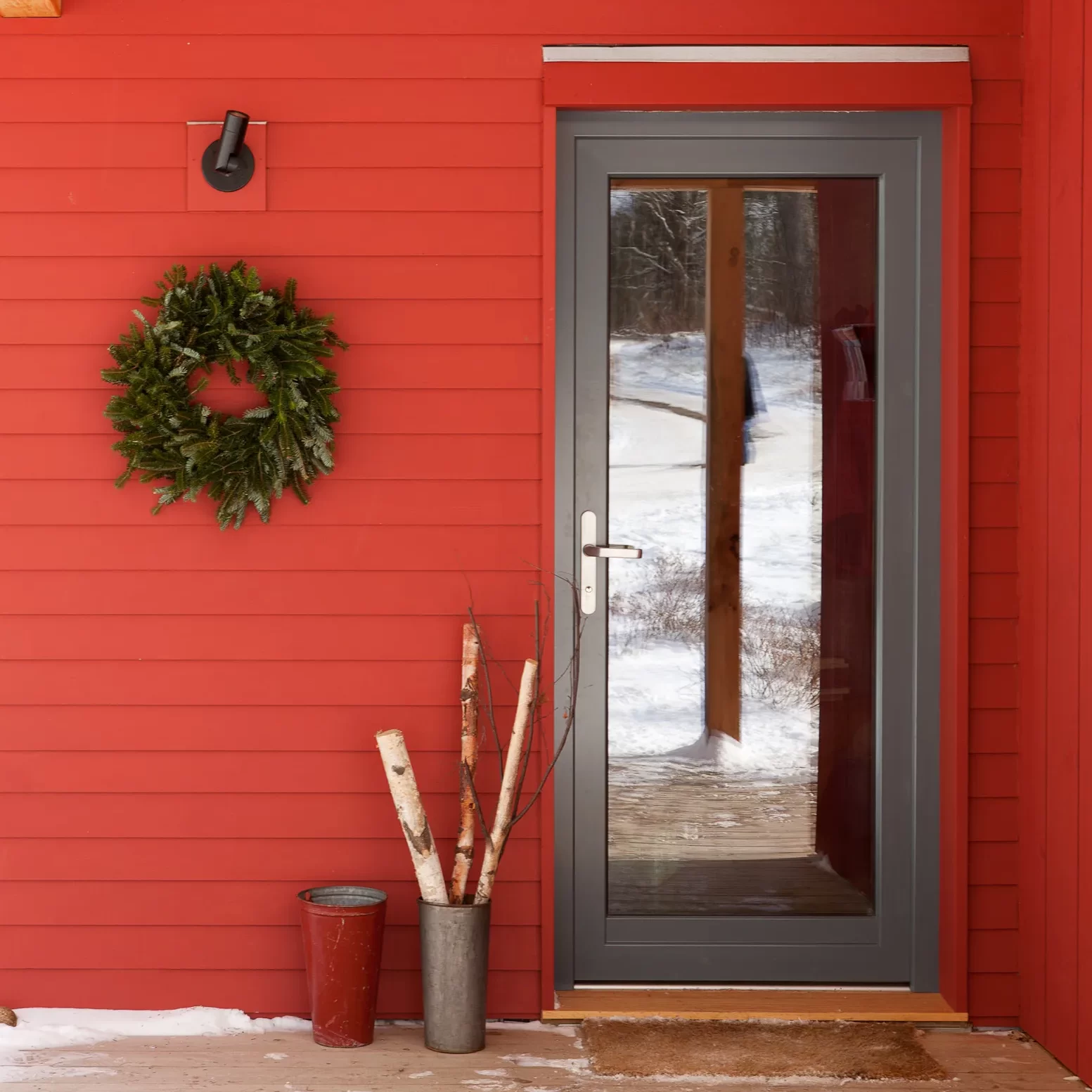
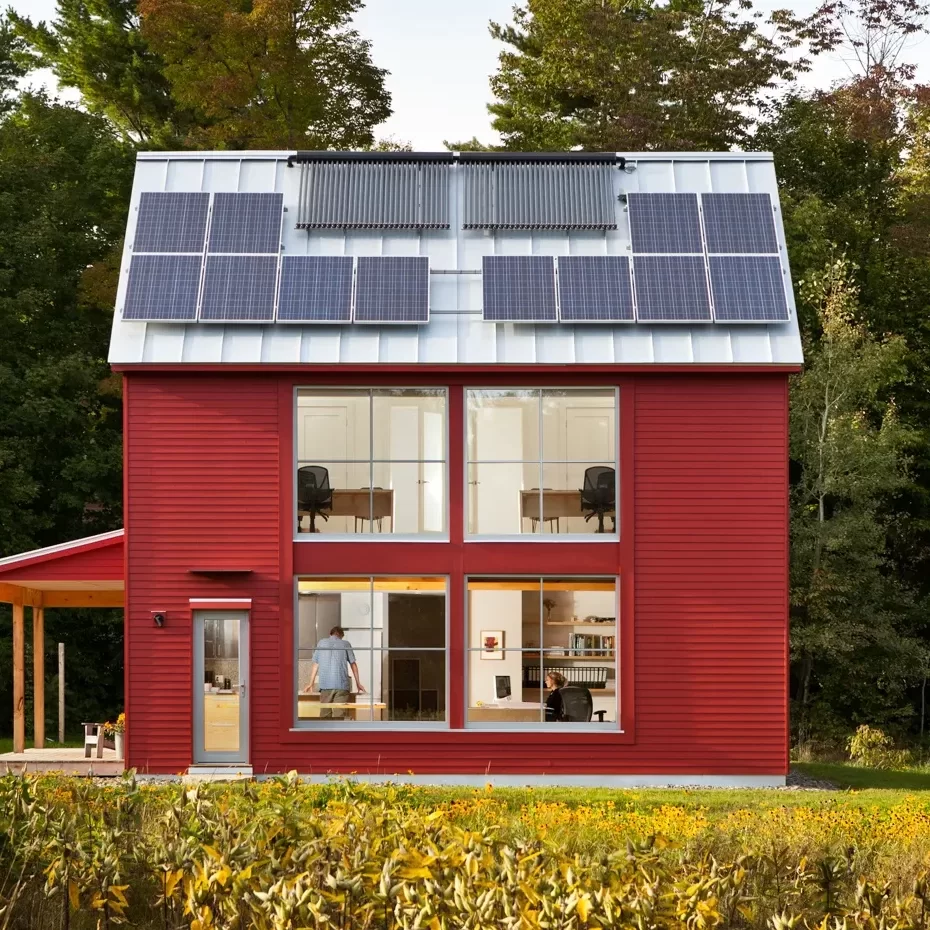
First Certified Passive House in Maine: The GO Home
When we founded our firm in 2008, the climate crisis was just emerging as an issue for architects. But it was clear to us even then that the status-quo response—promoting incremental improvements to building efficiency—was woefully inadequate. Meeting this epochal challenge would require a radical reduction in energy use and carbon emissions, and we dedicated our firm to achieving that goal. We chose as our model for energy performance the Passive House Standard, the most rigorous framework for maximizing building energy efficiency and indoor air quality. To develop and demonstrate the innovations required to achieve this quantum leap in performance in a cold climate, we built the first certified Passive House in Maine and the 12th in the U.S.: The GO Home.
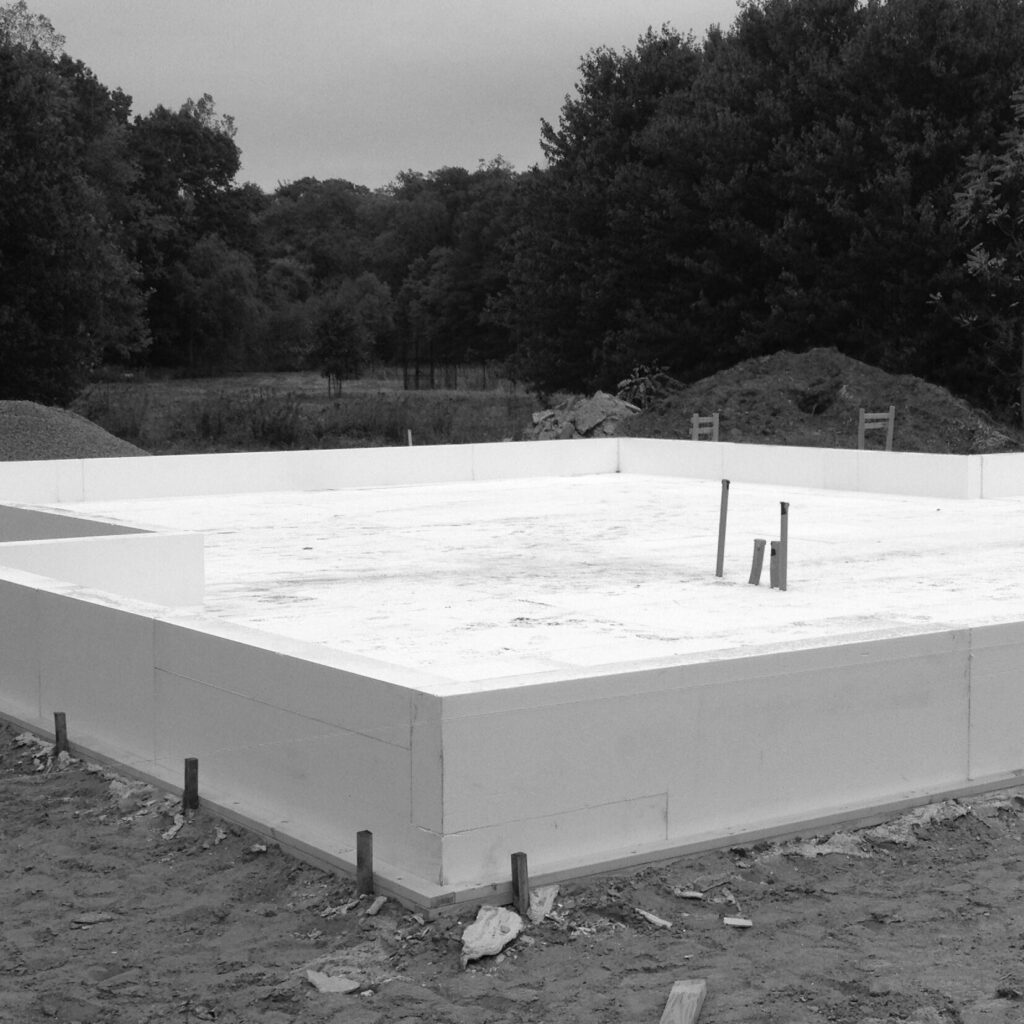
Patented Slab on Grade Foundation
In high performance buildings, slab foundations make sense from a number of standpoints. Compared with frost wall foundations, they use less concrete, which has an extremely large carbon footprint. They cost less, involve less digging, and avoid the thankless task of keeping water out of a New England basement. The result is a foundation that installs quickly and cleanly, supports virtually any residential-scale framed structure, and meets the stringent Passive House energy efficiency standard. The 50 percent savings in labor required for our slab system more than offsets the cost of the additional thickness of insulation, making it less expensive to construct than a conventionally built slab, and the insulation lowers operating costs for the life of the building. Our goal, in all the buildings we design, is to avoid the use of high-embodied-carbon materials, including concrete and plastic foam. Where suitable replacement materials are not yet available—primarily in ground-contact applications—we employ concrete and foam strategically and sparingly, striving to minimize their impact on the building’s overall carbon footprint.
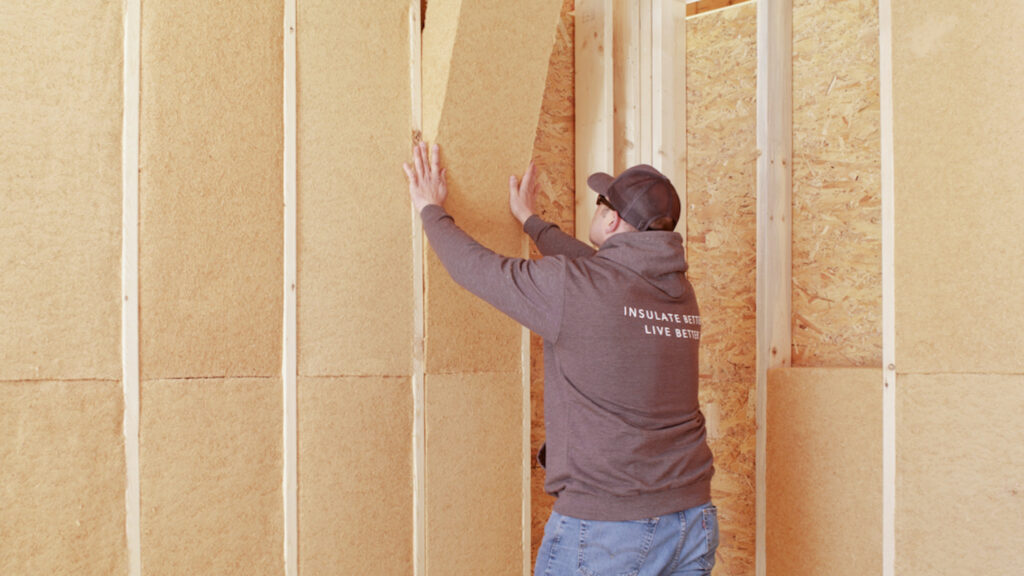
Wood Fiber Retrofit
Residential energy use accounts for 20 percent of energy-related CO₂e (Carbon Dioxide equivalent) emissions in the U.S., more than 1 billion metric tons annually, an amount comparable to the total emissions of Brazil, and exceeding those of Germany. Addressing the climate crisis requires that we significantly reduce the carbon footprint of the residential buildings we design and construct. But new buildings represent only the tip of the iceberg. The benefits to be realized by reducing the carbon footprint of these buildings–most of which are poorly insulated or uninsulated–are enormous. Upgrading the wall and attic insulation in existing residential buildings alone would reduce CO₂e emissions by 575 million metric tons annually, cutting housing’s share of total U.S. emissions in half.